Noticias
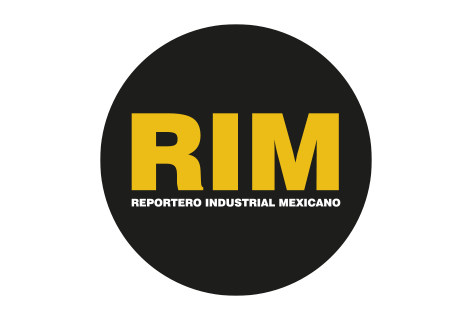
Los sistemas de cambio rápido mejoran los procesos metalmecánicos, reducen tiempos improductivos y mejoran la eficiencia operativa en centros de torneado y fresado.
En la industria metalmecánica, los tiempos improductivos asociados al cambio de herramientas representan un desafío constante para las empresas que buscan optimizar sus operaciones.
Lea también: La IA mejora la funcionalidad de los PLCs
La implementación de sistemas de cambio rápido ha revolucionado los procesos en centros de torneado y fresado al permitir reducir tiempos de preparación y maximizar la productividad.
El cambio rápido de herramientas es una solución que responde a las necesidades de flexibilidad y precisión en procesos de manufactura avanzada.
Este tipo de sistema, basado en interfaces modulares, permite realizar configuraciones múltiples con una sola herramienta básica.
Un buen ejemplo es el sistema Coromant Capto, del fabricante de herramientas sueco Sandvik, que tiene una interfaz cónica poligonal diseñada para ofrecer una alta rigidez y estabilidad, minimizando las vibraciones y mejorando la calidad del mecanizado. Además, su precisión de repetibilidad, con tolerancias de ±2 micras, asegura consistencia en los resultados.
La metodología SMED (Single-Minute Exchange of Die), que busca reducir los tiempos de cambio a menos de un minuto, encuentra en estas tecnologías un aliado estratégico.
Los sistemas modulares como Coromant Capto facilitan la separación de operaciones internas y externas, permitiendo que la preparación de herramientas se realice mientras las máquinas están en funcionamiento.
Esto no solo optimiza los tiempos de producción, sino que también elimina ajustes innecesarios y mejora la flexibilidad operativa.
Otra ventaja clave de estos sistemas es su integración con soluciones automatizadas. La incorporación de robots para el cambio de herramientas ha incrementado la autonomía en las líneas de producción, habilitando ciclos más largos y minimizando la intervención manual.
Este nivel de automatización se complementa con herramientas equipadas con sensores inteligentes, capaces de monitorear en tiempo real parámetros como desgaste y condiciones de corte, lo que permite una gestión predictiva y prolonga la vida útil de los equipos.
En términos de beneficios operativos, los sistemas de cambio rápido no solo reducen tiempos muertos, sino que también optimizan el uso de recursos, disminuyen costos y mejoran la calidad del producto final.
Estas soluciones son especialmente relevantes en sectores como el automotriz, aeroespacial y médico, donde la precisión y la capacidad de adaptarse rápidamente a cambios en los diseños son esenciales.
La tecnología Coromant Capto, aunque no es la única en el mercado, ejemplifica muy bien cómo las innovaciones en cambio rápido están transformando la manufactura.
Al ofrecer una solución versátil y eficiente, este sistema permite a los fabricantes maximizar la productividad en centros de mecanizado CNC, mejorando indicadores clave como la tasa de utilización de las máquinas, la calidad del mecanizado y la reducción de costos operativos.
En un sector donde la competitividad depende en gran medida de la capacidad para optimizar procesos, los fabricantes de herramientas están en constante búsqueda de soluciones que impulsen la eficiencia operativa.
Indicadores como la disponibilidad de máquinas, los tiempos de ciclo y los niveles de calidad son fundamentales para medir el éxito de estas tecnologías.
Sistemas como los de cambio rápido no solo contribuyen a alcanzar estos objetivos, sino que también refuerzan la capacidad de las empresas para adaptarse a un mercado cada vez más exigente y dinámico.
Otros artículos de interés
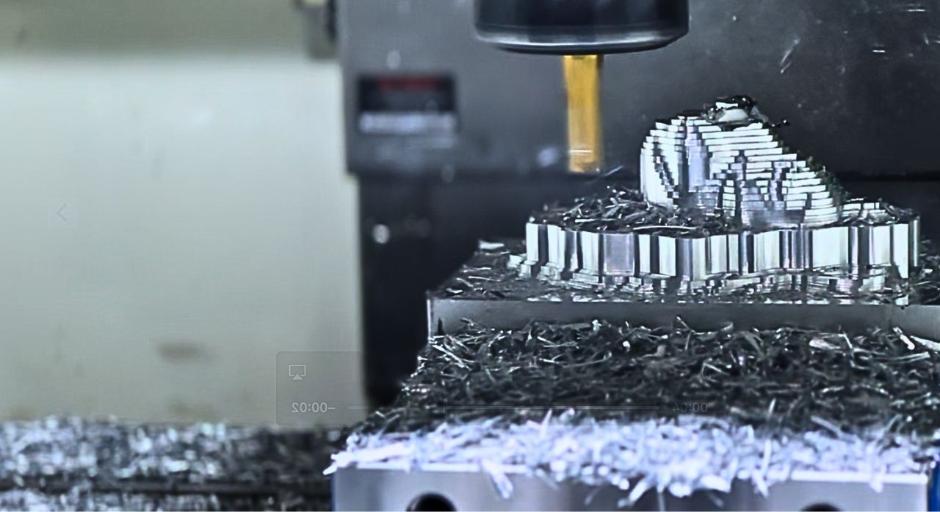
Herramientas de corte: Mayor valor para el maquinado aeroespacial
La industria del maquinado para componentes aeroespaciales en México continúa desarrollándose y

Lubricación: generador de eficiencia en planta
La lubricación influye directamente en la vida útil de maquinaria y en
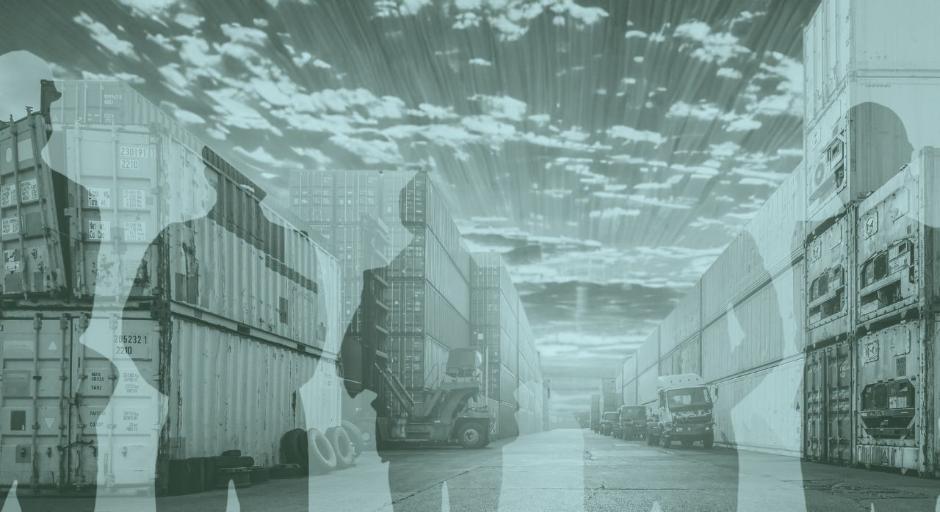
Ante aranceles, ¿qué papel juegan los organismos bilaterales?
La presión política sobre el comercio internacional ha incrementado de manera notable

La digitalización en mantenimiento reduce fallas en planta
En la industria actual, mantener las máquinas en funcionamiento no basta. La transformación
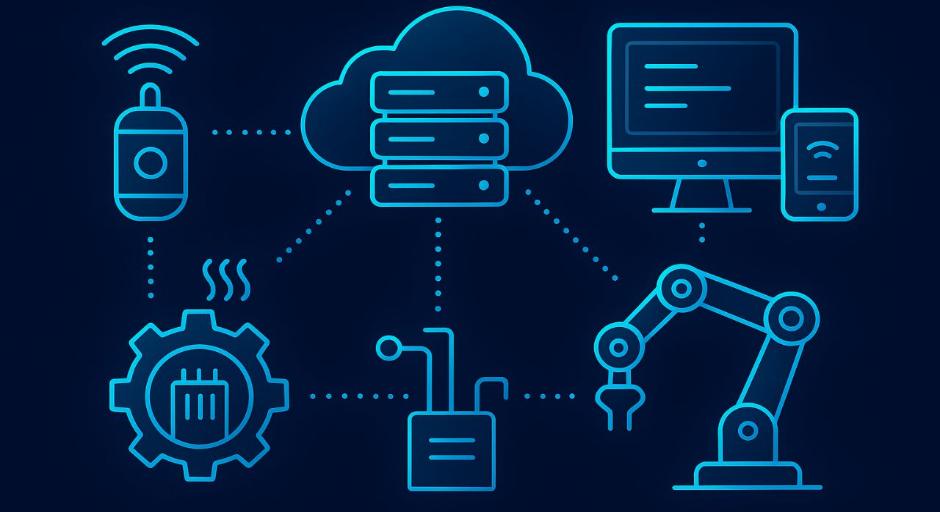
Se transforma la seguridad industrial con tecnología inteligente
La seguridad en las plantas industriales mexicanas ha vivido una transformación impulsada
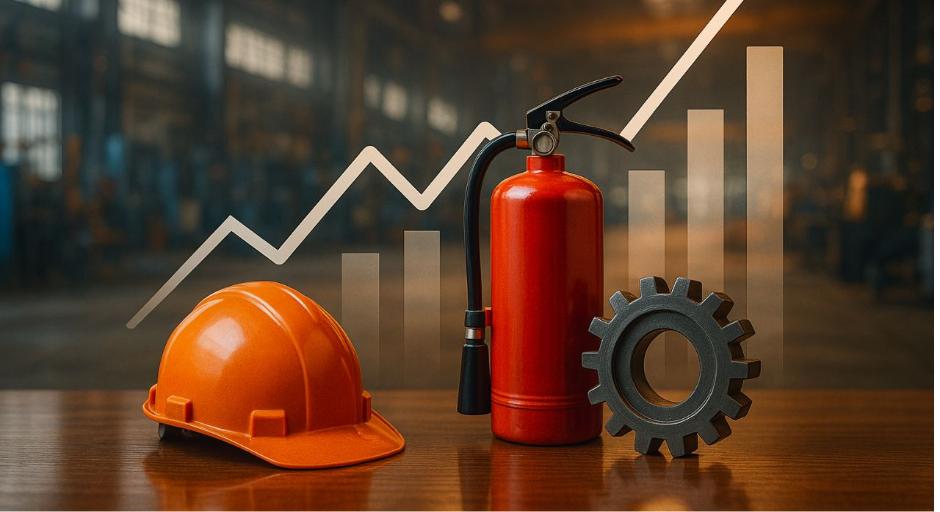
La seguridad industrial tiene un valor estratégico
La seguridad industrial es, y deb ser vista, como un componente estratégico